Buildings
Five, sunny all around apartments, in two separate buildings.
Large, well-demarcated private gardens, terraces.
Apartment central heat pump, mechanical ventilation.
Active virus, bacteria, allergen filtration, moisture treatment.
Comprehensive home automation ("smart home") system.
Car parking, room in garage. Electric vehicle charging.
Spacious (8-person) elevator.
Renewable, natural, chemical-free building materials.
Premium quality built-in materials.
Expected handover: August 2025
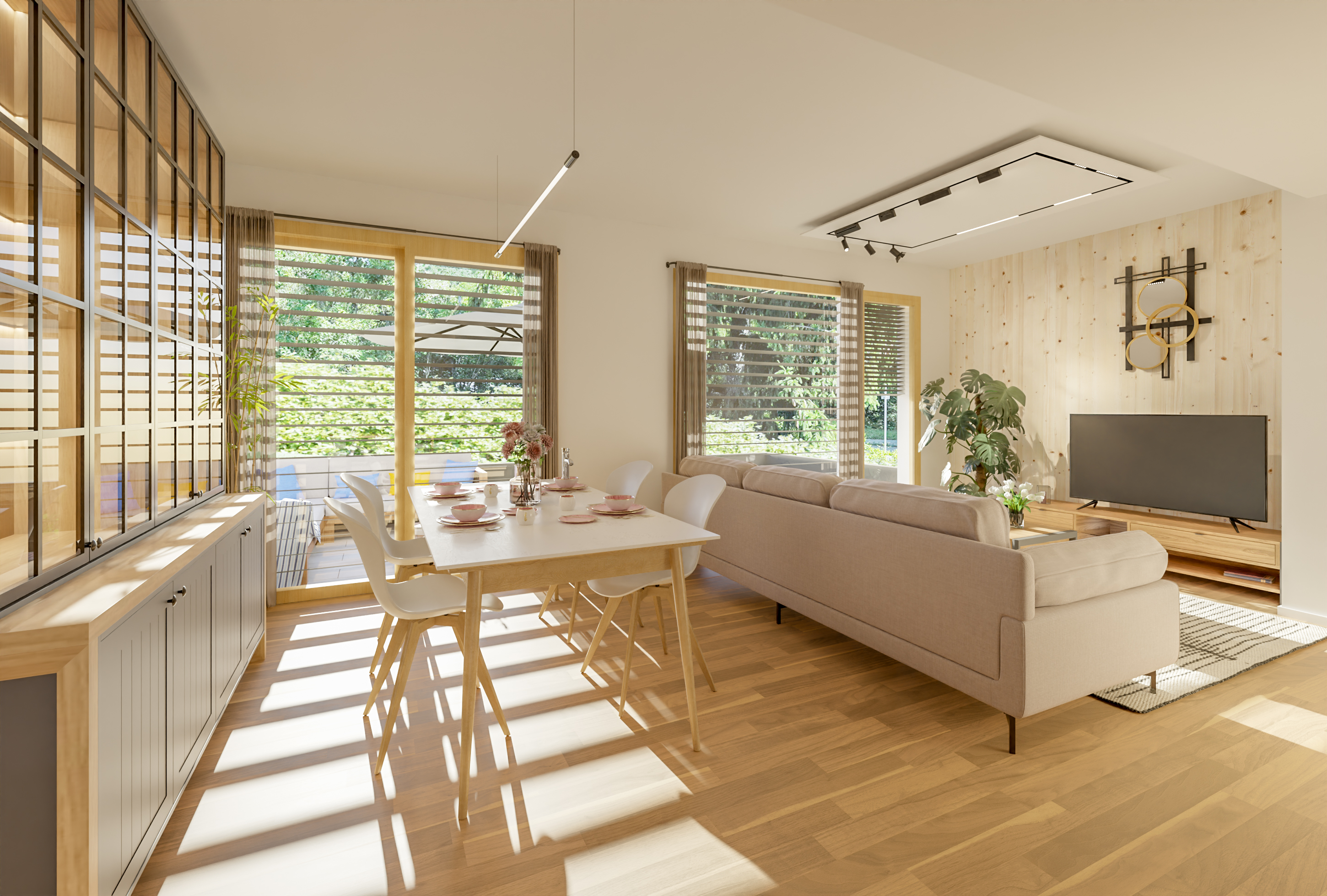
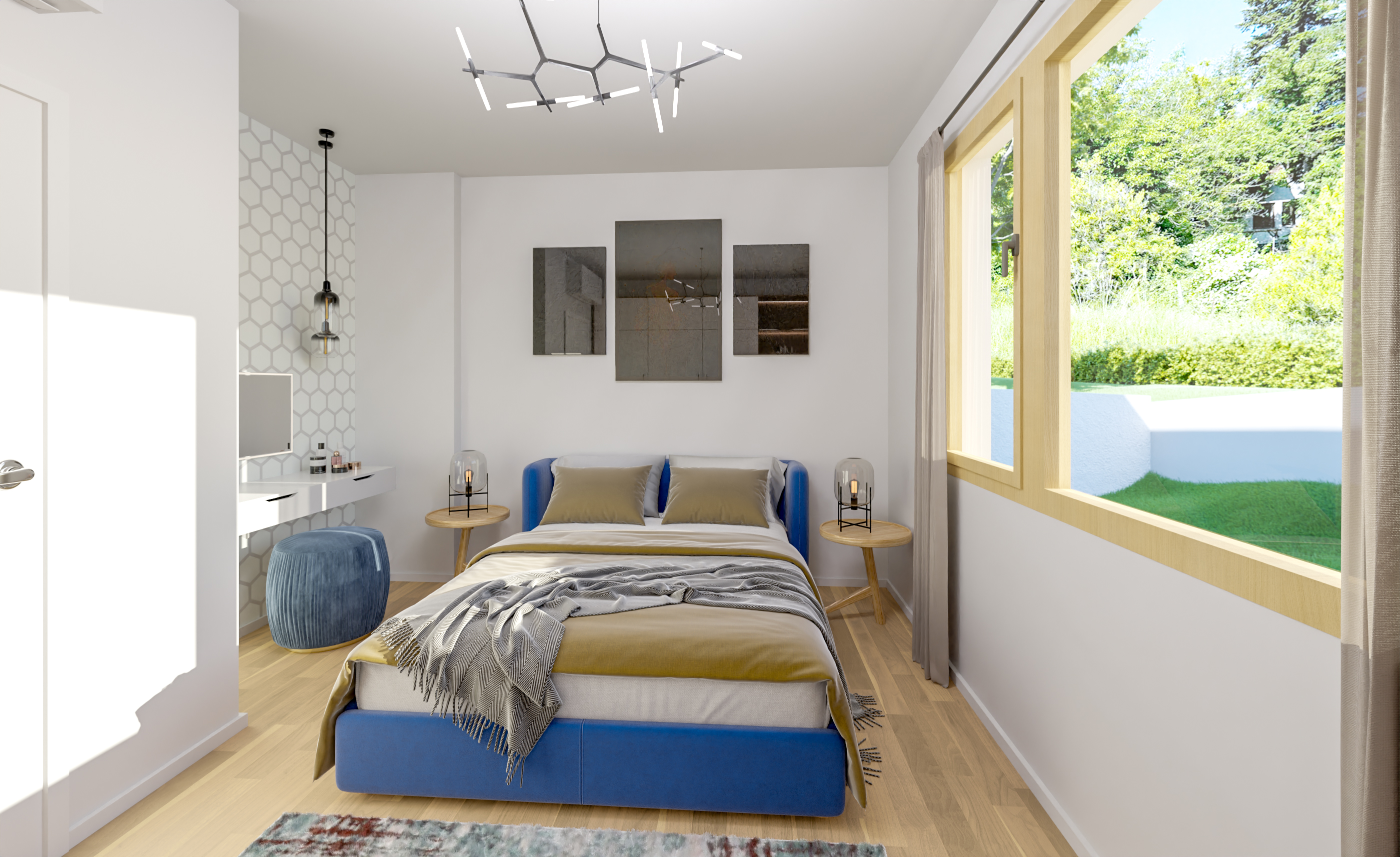
In accordance with the specific terrain conditions of the sizable plot, despite the higher expenditure, we made a decision to place the five apartments in two separate buildings, because in this way we were able to create several hundred square meters of well-separated, pleasantly situated, exclusively used garden areas for four apartments. The living room of the uppermost apartment (A3) opens onto a large, retracted terrace on the south side. Each building level belongs to one sun-drenched apartment. There are no wall neighbors.
Electric car chargers assigned to the meter of the respective apartment will be installed for the parking spaces located in the lower-level garage, which can be accessed on a flat driveway. The upper floors can be reached by a spacious, 8- person elevator in the natural light stairway.
The supporting structure of the building was built with the explosively popular, environmentally friendly CLT (Cross Laminated Timber) technology. The application of the Austrian development, which appeared in the 1990s, does not involve any compromises compared to traditional building materials. The panels made of high-quality Alpine pine tree, with cross-layering, result in a strong, yet flexible material, which, thanks to software-controlled preparation results in a perfectly dimensionally accurate, airtight structure. Minimal energy and not a drop of water are used during production and construction. No waste is generated.
The weight of the solid wood panel is about 70% of the weight of a traditional brick wall. It is a solid, not lightweight structure! Thanks to its flexibility, it is extremely resistant to seismic forces. Therefore, and due to the rapid execution, it played a significant role in the reconstruction after the Fukushima earthquake.
Due to the same flexibility, the echoing, knocking sounds known from rigid reinforced concrete structures do not occur here. Furthermore, thanks to these advantageous properties, buildings approaching a hundred meters in height are already being built of CLT (e.g. HoHo Tower, Vienna).
Perhaps surprisingly at first hearing, the fire protection rating of CLT panels is also adequate. In the event of a fire, the surface charring closes off the path of oxygen to the inside of the panel, thus preventing it from burning through. A 15 cm thick rock wool insulation is placed on the surface of the panels, which is the only natural insulating material with an A1, "non-combustible" rating. The fire safety classification of our building is: Low Risk.
The negligible carbon footprint of the purchased apartment - compared to traditional construction - can mean a significant tax advantage in the event of a future sale, contributing to the long-term value of the property.
In the Central European region, it is typical that the wood surface is not, or only slightly, left exposed. The walls are mostly (..completely on request) homogeneous, light surfaces. Typically, we planned to leave exposed wood surfaces on one wall of the living room and some walls of the traffic area, which in itself is extremely decorative.
The construction of the CLT structures is carried out by the wood building department of our Contractor partner:
Each apartment is equipped with its own, external air heat pump system for cooling and heating, the outdoor units are located away from the apartments. The discounted consumption (H tariff) can be measured individually on a separate electricity meter. Hot water is produced by a central heat pump, for efficient availability, which is connected to a 1000 liter storage tank. Water consumption is also billed based on individual metering.
The pleasant temperature in the apartments is ensured by indoor units installed above doors, or recessed into the ceiling, in living rooms. Thus, they do not interfere with furnishing at all. Unlike air conditioners, they do not blow, but slowly circulate the desired temperature air, virtually silently. Thanks to the built-in presence sensors, they avoid the people staying in the room. Mitsubishi's residential products have already proven in several of our completed buildings that beside their extremely economical operation we really only feel that the desired temperature is evenly perceptible in the room. Significant advantages over surface heating and cooling are that it can quickly restore the temperature of the interior air, if the apartment cools down or heats up, and it also performs effective dehumidification, with the resulting condensed water being drained into the sewer system, saving the residents from any damp feeling in the summer heat. In the winter, the enthalpic (moisture-recovering) ventilation system takes care of avoiding dry air. Both the ventilation and the cooling- heating system contain modern plasma filters, which completely filter out the allergens, bacteria, viruses and other harmful contaminants. The operation and maintenance of the devices is extremely simple.
Electric heating mats take care of tempering the cold floors - with discrete consumption. Electric, wall-mounted towel drying radiators are placed in the bathrooms.
Each apartment has an outdoor water tap and sockets. The garden is watered by an automated system, with a discounted tariff (without sewerage charges).
Blinds of the bedroom ensure the possibility of complete blackout, while aluminum slat blinds provide partial or full shading of the living rooms and other rooms, with electric control in each case.
The programming and remote access of the shading devices, car chargers, lighting, cooling-heating system, audio, alarm, door entry and access control system are solved via a home automation ("smart home") system, which can be expanded with additional functions according to individual needs. Weather data is provided by a meteorological station located on the roof.
The public area fence of the building - similar to the balcony railings - is made of steel bars, with a natural stone base and inserts. The waste storage is located away from the buildings, in an easily accessible but not disturbing location.
CLT Panel
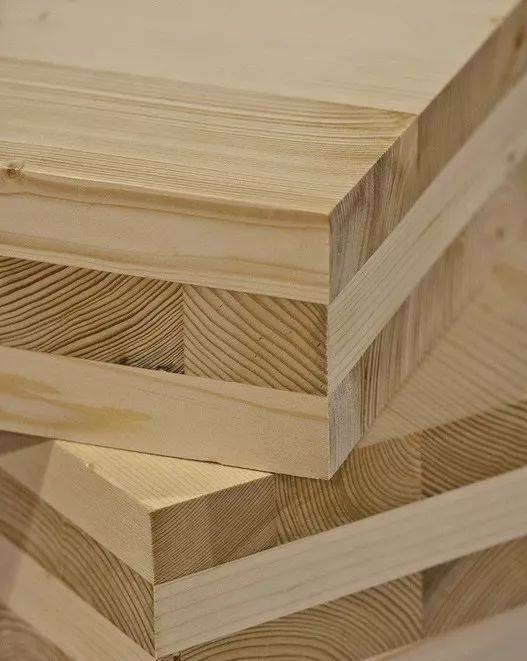
CLT Structure
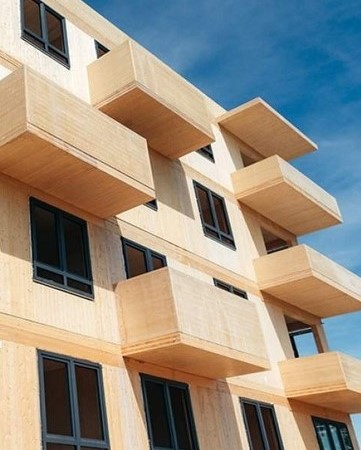
HoHo Tower
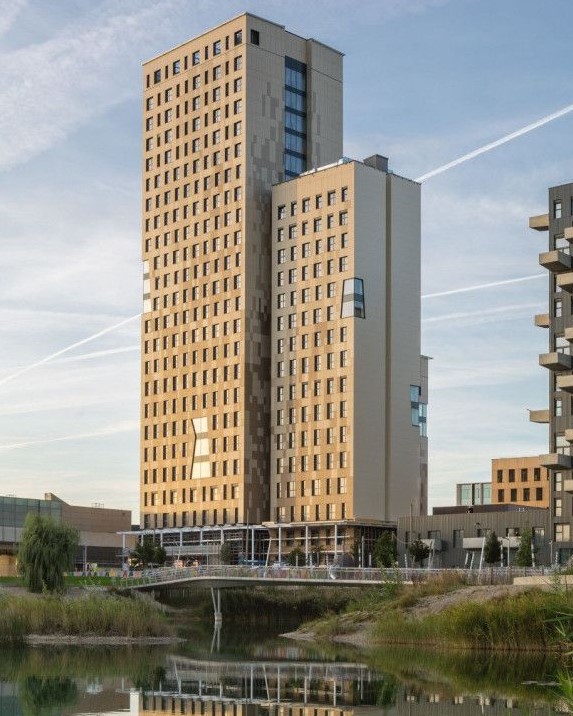